At its core, CNC milling involves the elimination of product from a workpiece with a collection of coordinated activities. Once the design is completed, the operator utilizes computer-aided manufacturing (CAM) software to equate the CAD design into a set of directions that the CNC device can check out, commonly in the kind of G-code.
One of the standout features of CNC milling is its convenience. Unlike traditional milling equipments, which usually run along one or two axes, CNC milling makers can operate on numerous axes at the same time-- typically 3, 4, or even five.
Check out cnc milling guide the transformative globe of CNC milling, an innovation that incorporates accuracy and automation to produce premium parts successfully from numerous products, and uncover its processes, advantages, and essential considerations for success in contemporary manufacturing.
The option of devices is one more vital aspect of CNC milling. The suitable tool option can substantially affect the high quality of the finished item and the effectiveness of the machining process.
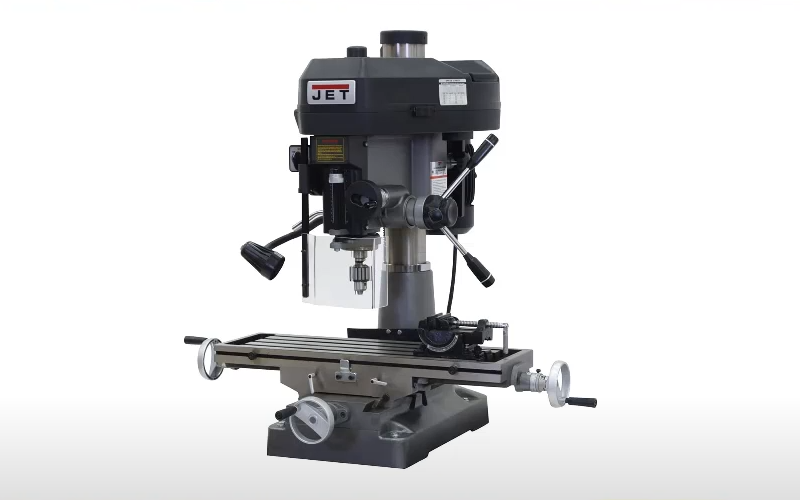
One essential element to think about in CNC milling is worldly compatibility. Recognizing the homes of the material, including its firmness, machinability, and thermal conductivity, allows operators to optimize the milling procedure and attain remarkable outcomes while reducing wear and tear on tools.
Beyond the technical aspects like layout, tooling, and products, there are additional factors to consider for optimizing CNC milling operations. Utilizing advanced attributes such as toolpath optimization techniques can improve the milling procedure additionally, allowing quicker machining cycles and decreasing waste.
One of the considerable advantages of CNC milling is the ability to automate recurring jobs, which reduces human mistake and enhances manufacturing uniformity. While conventional milling makers require a competent driver to oversee the production process, CNC milling makers can run neglected, performing pre-programmed directions with precision. This level of automation not just enhances performance however also liberates knowledgeable workers from mundane jobs, allowing them to focus on more beneficial activities such as quality assurance and process enhancement.
Regardless of its advantages, transitioning to CNC milling is not without difficulties. Initial financial investment can be substantial, with expenses associated with getting CNC makers, software application, and competent personnel training. Nonetheless, numerous businesses discover that the long-term cost savings associated with boosted productivity, decreased product waste, and boosted product top quality outweigh the preliminary costs. The accessibility of renting options and budget-friendly entry-level CNC milling equipments has made it a lot more accessible for mid-sized and tiny companies to embrace this technology.
Training and skill growth for personnel operating CNC milling devices are also crucial for making the most of the return on investment. Operators require a strong understanding of both the CNC maker itself and the software program being used for shows and surveillance. Lots of makers find success by giving in-house training programs or partnering with outside training organizations to outfit their teams with the needed skills and knowledge.
In recent years, technical improvements continue to form the field of CNC milling. As sectors progressively turn to automation, incorporating features such as man-made knowledge (AI) and device understanding into CNC makers can further enhance the accuracy and performance of milling operations.
Additionally, innovations in software application are constantly tightening the void in between design and manufacturing. Modern CAD/CAM systems now provide more intuitive user interfaces and improved simulation capabilities, permitting drivers to picture machining processes before they are implemented. By identifying prospective issues in the layout stage, companies can settle style flaws or maximize cutting approaches without sustaining costly changes to physical materials.
In the context of CNC milling, sustainability is additionally acquiring relevance as producers seek ways to minimize their ecological impact. Carrying out techniques such as optimizing cutting specifications, making use of more effective tooling, and reusing products can add to a more sustainable milling operation. Additionally, innovations such as additive manufacturing are being checked out in conjunction with CNC milling, presenting opportunities for hybrid manufacturing approaches that better boost sustainability by lessening waste.
Check out benchtop milling machine the transformative world of CNC milling, a technology that combines accuracy and automation to create top quality parts effectively from various products, and discover its procedures, benefits, and essential factors to consider for success in contemporary production.
In verdict, CNC milling represents an essential possession in modern production, providing business with the capacity to produce complicated and top quality elements successfully. Understanding CNC milling begins with a solid structure in its procedures, including the interplay in between layout, tooling, products, and software. Ultimately, successful combination of CNC milling equipment, proficient labor force training, and clever automation leads the means for the future of production, where effectiveness, high quality, and sustainability become the hallmarks of functional excellence.